Using your time and attendance system to minimize labor costs has never been more valuable.
Workforce management solutions like Oracle Cloud Time and Labor are one critical piece to control labor costs. The time clock you choose to use with your time and attendance software is another indispensable tool to manage direct and indirect workforce costs.
Employee Time Clocks for Busy Environments
All the benefits of using an employee time clock to collect time and attendance data are lost if it isn’t functional. Your time and attendance terminals need to have as much uptime as you expect from the machinery on the manufacturing floor.
.jpg?width=600&height=140&name=TimeCom_ExploreNewFeatures_600x140%20(1).jpg)
Durability for the manufacturing environment.
You need terminals constructed from quality materials designed to function in a non-office environment. Heavy machinery operating simultaneously creates vibrations, extreme temperatures, and debris that can degrade low-quality terminals.
Using an employee time clock like Accu-Time Systems Maximus Severe Duty integrated with the TimeCom for Oracle solution would be the perfect fit for cold, moist or dusty environments that need a reliable solution.
Operational if network goes down.
The average duration of Internet downtime is 4.78 hours. So there’s a high chance you’ll have a shift change while your Internet goes down. A high-quality terminal has enough memory to store a shift change’s worth of data, which it can then deliver to your back-end system once the Internet is back up.
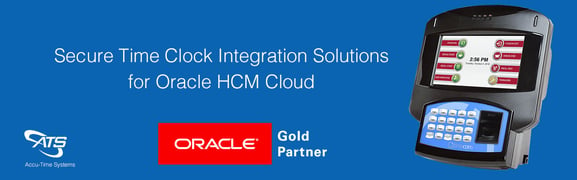
Don’t forget about that power source!
The terminal should have a battery power source, so it continues to operate during a power outage. When a time clock has its own temporary power source, it can collect data during the outage, avoiding data gaps when tracking employee time.
Enables speedy shift changes.
Your time clock’s throughput is how quickly it handles shift change. A clock that can’t process workers’ punches efficiently costs you productive time and extra payroll.
Workers waiting to clock-in delay the shift from reaching full capacity. Requiring workers to arrive early, so they can all clock-in before shift starts carries costly risks. When employees must wait in long lines to clock out, it increases their paid time.
Using the Time Clock for Improved Productivity & Lower Labor Costs
Integrating your time and attendance solution into your workforce management system gives your company more tools to control workforce costs.
Employee scheduling tools analyze hour worked data collected at the time clock, which helps you avoid over or understaffing the floor.
A sophisticated time clock also:
- Captures worksite location
- Allows workers to specify the job or department they will clock in for work
Using a time clock that collects more granular data helps identify outlier employees, shifts, managers, lines or other variables. The more precise the analysis becomes, the more accurately and effectively you can implement solutions to improve productivity and contain costs.
Maximize ROI with the Right Time Clock
The time clock is the first stop in your workforce production line. The terminal your company selects impacts how well your back-end systems, like Oracle Time and Labor, can do their jobs. It impacts the accuracy of your payroll software and schedule forecasting. Give as much consideration to selecting your time and attendance software and its time clock as you do any piece of machinery on the line.
Get in touch with our solution consultant today for all your time clock needs.
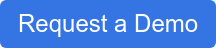
Check out other Time and Attendance Resources:
What You Need to Know about Stopping Time Theft and Buddy Punching
Why Payroll Processing begins at the Time Clock
Should I use my Mobile Device or Web Clock for Time and Attendance?
